Foam Moulding: Transforming Innovation in Diverse Applications
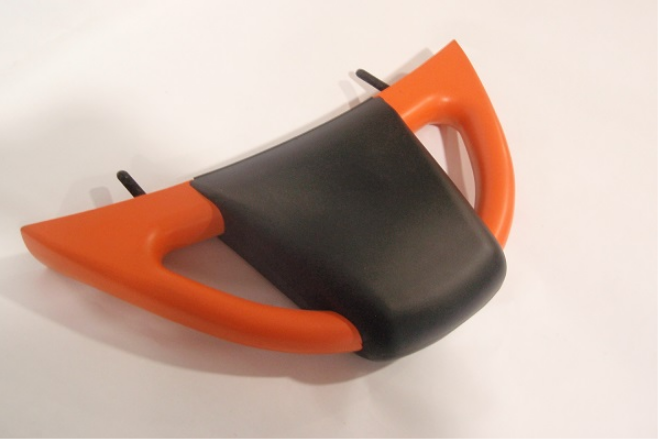
Foam moulding, particularly polyurethane foam moulding, represents a significant leap in material technology, blending versatility with performance. At its core, foam moulding involves the transformation of foam materials into specialized products through advanced techniques. Acoustafoam, with its 36 years of expertise in polyurethane moulding technology, stands at the forefront of this innovation. This article delves into the intricacies of foam moulding, highlighting its benefits, applications, and the specialized services provided by Acoustafoam.
Understanding Foam Moulding
What is Foam Moulding?
Foam moulding refers to the process of creating foam products by shaping foam materials using various moulding techniques. This process not only enhances the physical properties of foam but also tailors it to meet specific application needs. Polyurethane foam, known for its flexibility and durability, is particularly prominent in foam moulding. The process involves mixing chemicals that react to form a foam with desired characteristics, such as hardness and texture.
Key Characteristics of Polyurethane Foam Moulding
Polyurethane foam moulding can produce products with integral skin surfaces. This means that the foam has a tough, flexible outer layer that provides resistance against wear, tear, and abrasion. The core of the foam, which can vary in hardness from 30 to 90 Shore A, offers additional cushioning and support. This dual-layer construction makes polyurethane foam ideal for a wide range of applications, from automotive parts to furniture components.
Read Also: Fitted Bathrooms: Elevate Your Space with Customized Elegance
The Foam Moulding Process
Production Techniques
The foam moulding process at Acoustafoam involves several critical steps:
- Mixing and Dispensing: Two components of polyurethane foam are mixed and dispensed into a mould. The chemical reaction causes the foam to expand and fill the mould.
- Curing: Once the foam is dispensed, it needs time to cure. The curing process solidifies the foam, allowing it to retain its shape and properties.
- Trimming and Finishing: After curing, excess material, known as flash, is trimmed away. The final product is then stored until it reaches full cure.
- Quality Control: Throughout the process, quality control measures ensure that the foam meets density, hardness, and other specifications.
Types of Foam Moulding Systems
Acoustafoam offers a range of foam moulding systems, including:
- Integral Skin Foam Moulding: Known for its tough, skin-like surface.
- Elastomers: Includes both rigid and flexible foam moulding.
- Impact Foam Mouldings: Focused on impact resistance and insulation.
Applications of Foam Moulding
Automotive Industry
In the automotive sector, foam moulding is utilized for components such as gear knobs, armrests, and headrests. The integral skin of the foam provides durability and comfort, essential for automotive parts that undergo frequent use.
Furniture and Interior Design
Foam moulding is widely used in furniture design, including seating, armrests, and decorative trims. The flexibility of foam allows for intricate designs and customizations, making it a popular choice for both residential and commercial furniture.
Marine and Safety Products
The marine industry benefits from foam moulding through products like headrests and safety equipment. The ability to incorporate metal inserts into mouldings enhances rigidity and strength, crucial for marine applications.
Gaming and Recreational Products
In the gaming industry, foam moulding is used to create comfortable and durable components for gaming chairs and other equipment. The customizable nature of foam allows for ergonomic designs that enhance user experience.
Benefits of Foam Moulding
Customization and Versatility
Foam moulding offers unparalleled customization. Whether it’s creating a unique texture or incorporating specific design features, foam moulding can be tailored to meet diverse needs. This versatility makes it suitable for a wide range of industries and applications.
Durability and Protection
The integral skin of polyurethane foam mouldings provides excellent protection against scratches, abrasion, and wear. This makes it ideal for products that need to withstand harsh conditions or frequent use.
Rapid Prototyping and Production
Acoustafoam’s expertise in rapid prototyping allows for quick turnaround times. This capability is essential for industries that require fast development and testing of new products.
Foam Moulding in Acoustic Solutions
Acoustic Barriers
Foam moulding is also integral in the production of acoustic barriers. These products are designed to reduce noise transmission and provide sound insulation. Acoustic barriers made from foam can be customized to fit various applications, including automotive, construction, and industrial environments.
Foam Conversion for Acoustic Solutions
Foam conversion processes, such as cutting and moulding, are employed to create acoustic solutions tailored to specific needs. This includes customizing foam for improved sound absorption and insulation in different settings.
Conclusion
Foam moulding is a transformative technology that enhances the functionality and performance of foam materials across various industries. With Acoustafoam’s extensive experience and expertise, foam moulding solutions are crafted to meet the highest standards of quality and innovation. Whether for automotive parts, furniture, marine applications, or acoustic barriers, foam moulding provides a versatile and durable solution.